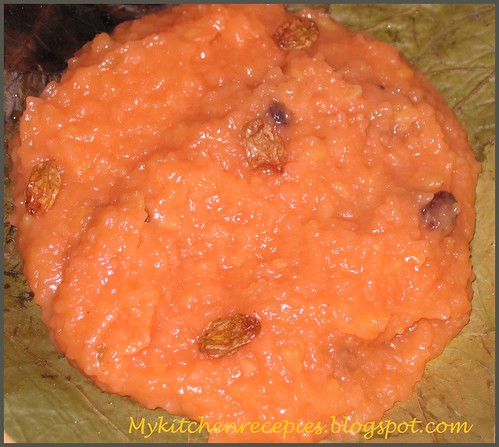
Two weeks before I saw this recipe in Rak's kitchen . This is one of my Favorite Sweet.But I totally forgot about this .During my college days I used to eat this Regularly.This is one of the famous prasadham in Chidambaram Natarajar Temple.I prepared this on new year.My husband & son Enjoyed this.I made small changes to the recipe.I used pinch of orange colour & Pacha karpooram (Borneo-Camphor). I just remove from heat & took these photos,so it looks Watery,once it turns cool,u will get perfect pongal.Here my recipe
Ingredients:
Rice- 1 cup
Moong dal - 1/2cup
Kalkandu - 1 1/2 cup
Milk - 1/2 cup
Water - 3 cup
Ghee- 5 table spoon
Cardamom - 3
Cashew- 10
Raisins- 20
Pacha karpooram- pinchOrange colour - pinch
Preparation method:
1. Wash Rice & Moong dal,add water along with it.Pressure cook for 8 whistles.
2. Add milk in rice mixture,mash well.
3. Add 2table spoon ghee in heavy bottom pan,roast cashew & raisins til it turns golden brown.
4. In same pan itself,add mashed rice,pinch of colour,Cardamom & Pacha karpooram,mix well.
5. Now add kalkandu in that.I used diamond kalkandu.so i added as it is.If it is bigger one break into pieces & add.
6. Mix well until it melts.Add remaining ghee while mixing.
7. Serve hot & Enjoy.
